Among the several sectors, including manufacturing, transportation, and construction, steel is a basic component. Worldwide, steel factories work to enhance their procedures to satisfy growing demand. These plants depend on advanced technology to increase output and efficiency. The section rolling mill is a very crucial element of such technology. It increases the production of steel…
Category: Featured Product
Factors Affecting the Performance of Steel Rolling Machines
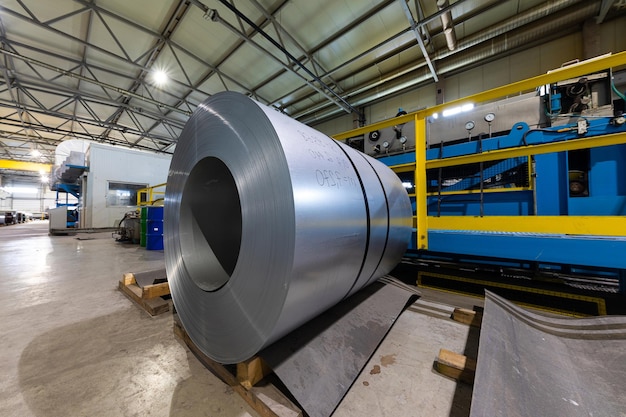
Metal at the steel mill in Bangladesh and other industries across the world is shaped in great part by steel rolling machines. Producing steel sheets, rods, and other parts calls for this equipment. Still, several factors influence the operational efficiency of the equipment. Understanding these components promotes higher production quality and helps to reduce downtime.
This article looks at the primary factors affecting steel rolling machine performance and offers suggestions on how to raise their efficiency.
Quality of Raw Materials
The raw material of a steel rolling machine greatly affects its performance. For instance, uneven rolling of machine components might be caused or damaged by inferior or irregular-grade steel. Premium steel is what makes good final goods and simpler procedures possible.
Furthermore, the raw material’s temperature is quite crucial. For best rolling, steel has to be heated to the right degree. In case the temperature is very low, the rolling process may prove ineffective or result in flaws.
Machine Upkeep
Effective operation of steel rolling equipment largely relies on regular upkeep. It is important to note that neglection of of maintenance results in worn-out components, poor performance, and even failures. Regular inspection of parts like motors, bearings, and rollers is really crucial.
For example, inadequately greased rollers provide unneeded friction that compromises both machine performance and product quality. Moreover, consistent cleaning helps to avoid the accumulation of trash and filth that could disturb activities.
Operator Skill
Another very important consideration is the operator’s degree of expertise. Early identification of any problems by skilled operators helps to modify machine settings for the best operation. While automatic controls abound in current steel rolling machines, human knowledge is still required to handle unanticipated problems.
Regular training ensures operators stay current on safety measures and the highest standards. Better-prepared staff is best to satisfy the complex demands of a steel plant in Bangladesh or elsewhere.
Machine Design and Technology
A steel rolling machine’s design and technology largely define its efficiency. Manufacturing rates might slow down if older equipment lacks the speed or precision of more modern units. Modern machines abound in complex components like faster rolling speeds and automatic thickness control.
Turning to advanced technologies might be expensive. However, companies must weigh the required investment against improved performance. Increasing production with high-tech equipment, for instance, reduces long-term running costs.
Environmental Conditions
Machine performance can be greatly impacted by environmental elements like temperature, humidity, as well as dust. For example, excessive humidity could lead to corrosion on machine components, while severe temperatures could affect the rolling action of the steel.
Keeping the surroundings neat and under control reduces these hazards. Furthermore, applying protective coatings on machine parts might help to stop environmental element damage.
Load and Usage
Moreover influencing the performance of a steel rolling machine is its weight. From overloading, a machine might overhear, wear and tear, or even mechanical failure. Actually, running the equipment in its suggested capacity is quite important.
Rotating work across numerous machines helps to prevent one unit from being abused. With this approach, the steel plants become more efficient.
Energy Availability
Power outages or voltage swings can interfere with operations, produce manufacturing variances, and perhaps destroy important machinery. These disruptions not only compromise machine performance but also could cause expensive downtime and maintenance.
Installing surge protectors, backup generators, or power stabilizers guarantees a consistent energy flow. For motors, heating elements, and other components, for example, constant energy flow guarantees their exact operation, therefore lowering mistakes and extending the lifetime of the machine. Energy management investments help to protect the general rolling process efficiency and productivity.
Wear and Tear
All machinery ages and steel rolling machines are no exception. Constant use gradually degrades parts like rollers, belts, and bearings—which can influence performance and produce lower-quality products. Ignoring this regular wear may result in unexpected downtime, costly repairs, or maybe equipment breakage.
Regular maintenance and scheduled replacements are absolutely vital to help to minimize these problems. Regular replacement of worn-out rollers or lubricating components, for example, helps to preserve the machine’s lifetime and maintain performance. While repairs and inspections can call for time and money, they save a lot by avoiding serious malfunctions and guaranteeing flawless, continuous output.
Endnotes
From the quality of the raw materials to operator capability and ambient conditions, several factors affect the operation of steel rolling machines. Steel plant businesses might boost output by stressing consistent maintenance, technical improvements, and worker training.
Solving these components will enable steel manufacturers to ensure improved operations and generate better products. Every step counts toward long-term success, from maintaining machinery in good condition to guaranteeing a constant energy supply.
Key Challenges in Operating Reheating Furnaces In Steel Plants
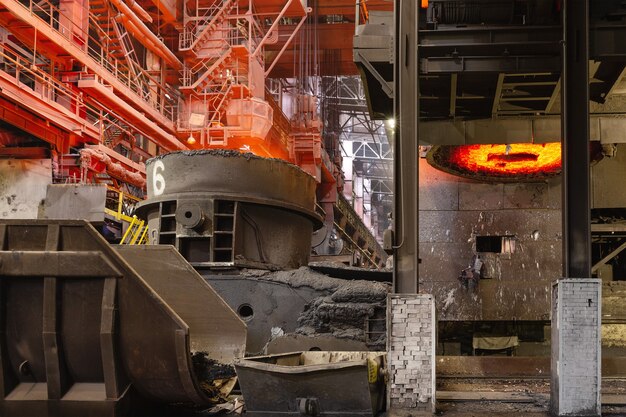
Operating reheating furnaces of rolling mills, especially at steel plants, is not an easy gig. Reheating furnaces are necessary and quite important as they treat steel billets, blooms, and slabs to the appropriate temperature before conducting the next stage of processes. The performance and the reliability of reheating furnaces have a direct influence on the quality of steel and the productivity of the plant in general. However, several issues are associated with the operation of these furnaces, and their mitigation is necessary to obtain optimal efficiency.
Let us look at all issues and their solutions in detail:
Temperature Control
One of the significant problems encountered in steel plants, and generally around the world, is temperature control: the heating furnace of rolling mills should have constant temperature control so as to attain correct mechanical properties through the heating range of this metal. Moreover, if the furnace is extremely hot or too cold, it can give subpar steel with uneven thickness or surface imperfections.
Solution: Modern reheating furnaces use hi-tech methods of temperature control. They comprise sensors as well as automated feedback systems designed to provide consistent heat distribution. Thereby preventing steel overheating or underheating. This equipment needs constant upkeep and calibration to guarantee accuracy.
Energy Consumption
Reheating furnaces consumes a lot of energy and hence may result in high operational costs. Steel plants in Brazil industries are currently hitting rock bottom regarding energy consumption but still maintaining efficiency in production. Poor insulation or old furnace technologies and fluctuation in operational loads are some reasons for energy ineffectiveness.
Solution: Some energy-saving measures that can be applied include improving the furnace’s insulation, utilization of more efficient burners, and waste heat recovery systems. Furthermore, optimal furnace operation through better load management as well as predictive maintenance helps to keep energy costs under control.
Furnace Lifespan and Upkeep
The reheating furnace of rolling mills serves under extreme temperatures, which, after long periods, can lead to the wearing of some parts. The longevity of the furnace relies on several factors, including the quality of the materials used, the frequency of their upkeep, as well as the operational conditions. Improperly maintained furnaces often result in breakdowns, which require huge amounts of money for repair work and downtime.
Solution: Preventive maintenance is the most important way to extend the furnace’s life. Periodic inspections, cleaning, and the replacement of worn-out parts help avoid major breakdowns. Advanced diagnostic tools can also be installed to monitor the performance of the furnace in real time before they become severe enough to result in an actual breakdown.
Emissions Control
Emissions from the reheating furnace, if not well managed, pose a challenge to steel plants. These furnaces usually give off gases of CO2, NOx, and particulate matter, which have adverse environmental impacts. Emissions are an issue that many countries regulate highly for steel plants, and these plants can get charged and their reputation damaged if they fail to meet emission standards.
Solution: The necessary reduction in the released emissions can be achieved by installing advanced technologies like flue gas desulfurization systems, selective catalytic reduction units, as well as electrostatic precipitators. A furnace’s combustion process also needs to be improved in order to increase the completeness of fuel burning so that, consequently, harmful emissions decrease in quantity.
Variability in Raw Materials
The quality of raw materials input in the furnace could vary from one batch to another, especially on billets or slabs. Such variations may affect the consistency of the heating process as well as the quality of the final product yield. Steel plants have to fight such a challenge that can lead to inconsistency among the products coming out of the plant.
Solution: High-quality, consistent raw materials are essential. Furthermore, automation of control systems of the reheating furnace of rolling mills allows for real-time readjustment of heating parameters according to the characteristics of the material coming in. This can thus minimize the effects of variability of raw materials on final product quality.
Furnace Safety
Working on reheat furnaces simply means high temperatures and significant potential safety risk. Explosions, fire, and burning of one’s clothes are just a few potential risks that demand attention.
Solution: For such high-temperature processes, safety precautions can call for the installation of automated shutdown systems, pressure relieving valves, as well as temperature sensors. Along with frequent safety inspections, internal training for operations, like how to do activities properly in a functioning plant, guarantees a safe workplace.
Automation and Control
Automation plays a significant role in the efficient operation of modern steel plants, but relatively complex problems arise during the integration of automation systems in the reheating furnaces of rolling mills. The furnace itself has a complex nature that requires hi-tech control systems, and any failure in the automation system may disrupt the whole production line.
Solution: Investment in reliable, state-of-the-art automation and control systems will be important. Also, training operators to effectively handle automated systems with less chance of error will improve overall performance.
Endnotes
From regulating temperature and energy efficiency to managing pollutants and workers’ safety, running reheating furnaces of rolling mills in steel factories presents several difficulties. Still, many of these problems may be resolved with the required technology, frequent maintenance, and personnel training. Product quality will rise in tandem with operational efficiency development, thereby enabling steel factories to be more sustainable finally.
How Worm Wheel Gearboxes Enhance Efficiency in Steel Plant Operations
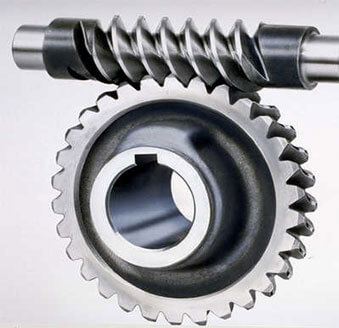
For the seamless operation of heavy activities, steel factories depend on the exact and most reliable machinery. Among them, the worm wheel gearbox is pretty important in raising efficiency. Like in a steel factory, this kind of gearbox is crucial for controlling power flow in several operations. Its unique architecture enables plants to operate better and be free from complications.
Let’s investigate these gearboxes’ working and their effects on steel plant’s operations.
About Worm Wheel Gearbox
Designed to move power between non-parallel shafts, a worm wheel gearbox is made up of two key components: the wheel (a toothed gear) and the worm, a screw-like construction. The wheel is driven by the rotating worm to turn, thereby slowing down the speed and raising the torque.
Under this arrangement, machines can manage heavy loads with low wear and tear. Furthermore, the gearbox is small, which makes it a great fit for constrained areas often found in manufacturing settings.
Why Are Worm Wheel Gearboxes So Important For Steel Plants?
Steel factories handle big machinery needing exact motion control. For rolling mills and conveyors, for example, dependable gear systems are essential for managing the strain of constant operation. Worm wheel gearboxes help with:
- With an excellent torque output, these gearboxes let machines easily manage big loads.
- Unlike other gear systems, worm wheel gearboxes run silently, therefore producing a safer and more pleasant workplace.
- Their tiny scale qualifies them for fitting in confined areas of steel industry equipment.
Though there are various kinds of gearboxes, the simplicity and efficiency of the worm wheel design really shine.
Improving Steel Plant Operations’ Effectiveness
Maintaining production and satisfying market needs in a steel plant in Oman depend on efficiency. Worm wheel gearboxes enhance the following areas of operation:
Accuracy in Movement
Complex operations, including rolling, cutting, and pressing—all of which depend on great accuracy to guarantee product quality—are part of steel manufacturing. Any small movement mistake could cause material waste or flaws in the steel goods. By guaranteeing precise and smooth power transfer, worm wheel gearboxes assist to increase motion control. Their design lets machines run with perfect accuracy, therefore lowering manufacturing line mistakes.
Energy Conservation
In any industrial activity, but particularly in steel mills where energy consumption is significant, energy efficiency is of first importance. Designed to reduce energy waste during the power transfer mechanism, worm wheel gearboxes effectively move power, therefore lowering friction and other energy-wasting elements. This makes certain that, with the same output, the plant uses less energy.
Durability
The lifetime of machinery is quite important in steel mills, where it works under harsh conditions, including high temperatures, large loads, and constant operation. Strong materials employed in worm wheel gearboxes enable their resistance against these high loads. Their strong construction assures their capacity to resist the usual wear and tear in industrial settings.
Advantages Over Other Gear Systems
- These are specifically beneficial for safety in heavy machinery- as their self-locking features stop reverse motion.
- Their design calls for less regular service, therefore saving time and money.
- These gearboxes are flexible as they can run both high and low-speed activities.
- Furthermore, their capacity to manage heavy-duty tasks makes them vital in steel fabrication.
Difficulties and Considerations
Worm wheel gearboxes have several restrictions, even if they provide certain benefits. For instance, friction creates heat that might call for cooling systems. Still, good lubrication and frequent maintenance help to reduce such problems.
Depending on their machinery needs, steel manufacturers also have to select appropriate gearbox specs. Using an undersized gearbox, for example, can cause performance problems.
The Future of Steel Plant Operations
Given the growing demand for premium steel, plants must remain competitive by means of consistent machinery. Worm wheel gearboxes will still be the most important factor in optimizing their operations. They are a sensible investment to increase efficiency.
Steel plants in Oman or elsewhere can use such advanced technology to boost output and alleviate downtime. When these gearboxes are used correctly, their benefits outweigh the drawbacks.
Endnotes
Perfect and flawless operations in steel mills depend on worm wheel gearboxes. They have excellent torque, precision, and durability—qualities absolutely necessary—for handling big machines. Moreover, their tiny size and self-locking mechanism make them a sought-after choice in many other fields all around.
In a steel plant, these gears have proved dependability in raising output. By using such robust technology, steel manufacturers may maintain their competitive edge as well as achieve long-term success.
Why Investing in Round Bar Straightening Machines Pays Off?
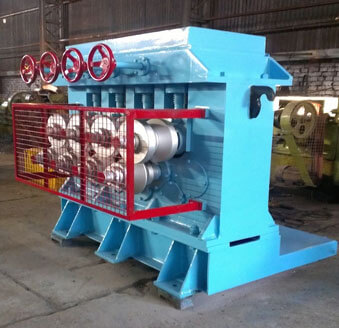
Industries relying on long-lasting, precision-crafted metal parts and components may well see high-quality equipment as the sole factor which makes the difference between achieving reliable and efficient production. Round bar straightening is one of the most critical tools, given that it is intended to straighten round bars to certain standards. This, therefore, assumes a very significant role in ensuring materials are of the right strength, usability, and appearance standards for industrial use. For sectors like construction, automobiles, and heavy manufacturing, which require proper quality control, an investment in a highly efficient round bar straightening machine will promote higher productivity with less waste.
Use of Round Bar Straightening Machines
Straightening round bars is an exacting process in that the size and length may vary, as well as their materials. RMT Tools offers a round bar straightening machine for accuracy and reliability. This plant would ensure each bar to be accurately adjusted with no possibility of warping or bending, among other structural weaknesses. With such automation of the straightening process, companies can speed up their production with great standards maintained.
Benefits of Straightening Machine
The benefits for the manufacturer of using a dedicated straightening machine include the following:
- Far greater quality uniformity than with hand re-straightening, thereby significantly reducing waste generation.
- Reduced manual handling content, resulting in better workers’ safety and lower labour costs.
- Utilization of RMT Tools’ expertise in designing long-lasting, rugged precision equipment, which will provide long-lasting performance in demanding industrial environments.
Rolling Mill Rolls Manufacturer in India- A Key to Efficiency and Quality
Roll quality is a significant factor in the rolling mill and are of utmost importance while forming, compressing, and smoothing a metal into various shapes in the form of sheets to beams. RMT Tools, one of the prominent producers of rolling mill rolls in India, deals with rolls that withstand extreme pressure and high-temperature changes. These rolls, being made of high-grade material, assist the manufacturer in achieving the smoothest, uninterrupted procedure in the production chain, as it is up to the desired standards of the industry.
High-quality rolls will not only help in reducing the downtime but will also lengthen the life of the rolling mill. This helps companies in the high-demand sectors to maintain a regular output without missing the production quotas and meeting the expectations of the customers. Quality is RMT Tools’ promise to ensure every roll is maximized in terms of durability and performance.
Why Invest in Quality Equipment?
To a large-scale manufacturing company, quality equipment is something that could be more pleasant to have. It’s a competitive advantage. Devices such as round bar straightening machines or rolling mill rolls make all the difference between high production speed, material efficiency, and final product quality. Reliable operation by the quality of the equipment allows companies to streamline the processing steps while reducing waste and achieving better, more consistent products.
Are you ready to help your production move to the next level? Contact RMT Tools for your advanced round bar straightening machines and high-quality rolling mill rolls.
What Makes RMT Tools Your Best Choice in Your Industrial Requirements?
RMT Tools, with decades of experience in the manufacturing and industrial equipment sector, has established a name in the finish machinery products for quality and reliability. Among the top manufacturers of rolling mill rolls in India, RMT Tools offers solutions to meet the industry’s severe requirements. From precision straightening machines to robust rolling mill rolls manufacturer in India, all its products are designed to achieve peak performance and product quality that helps companies succeed.
Explore RMT Tools’ full range of equipment to see how their equipment can make all the difference in your production efficiency and reliability. Invest in quality today for a more productive tomorrow.
Equipment decisions are vital when it comes to manufacturing. With RMT Tools’ assistance, businesses can create a basis of machinery that accomplishes the idealization of production goals and quality.